What is an inductor?
An inductor, also called choke coil, coil (air or iron coil), inductivity (here meant as a component) or inductive resistance, also inductive energy storage is a passive component in electrical engineering.
In the majority of cases, an inductor has only one winding (per phase). It can be designed as an air core coil or with a ferromagnetic iron core. Air coils are largely linear in terms of inductance, whereas coils with an iron core usually require an inserted air gap to linearise the characteristic curve (shear).
Inductors for power applications can be divided into alternating voltage inductors (AC inductors) and chokes for direct current circuits (DC chokes).
AC inductors can be of 1-phase or 3-phase design. As a rule, these are inductors with ferromagnetic cores, with or without air gaps. DC chokes can be designed as air coils or with iron cores.
The essential parameter of an inductor is its inductance.
It must also be designed for the expected continuous and peak current, if necessary for both the DC and the AC part.
Instead of an inductance specification, a voltage (drop) at rated current can also be specified (see line chokes, uk ..%). The rated frequency and the voltage to be taken into account for insulation are also required.
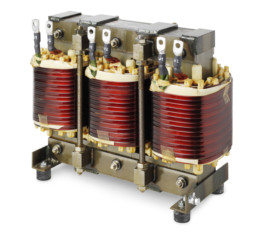
In industry and universities, a number of designations are used to structure inductors according to their intended use. These designations – seldom taken from a standard – classify inductors in a motley fashion according to their physical background, their construction, their cooling or their intended use:
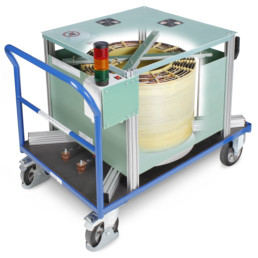
Line choke, commutating choke:
AC inductors for mains (base) frequency, mainly in 3-phase design; for improving the mains current load (PFC) and for reducing the edge steepnesses in the semiconductor valves of downstream power converters. These inductors are mainly used in drive technology for a voltage drop uk = 2…4%
Smoothing choke, chopper choke, DC link choke, load choke:
Direct current (DC) chokes, e.g. for the (wavy) DC circuit behind a rectifier, for the DC intermediate circuit in power converters between input rectifier and output inverter. Also for excitation circuits of generators. In power supply units, the current dependence of this “smoothing element” must be taken into account.
Even if the term of a direct current choke (DC choke) is widespread, the operating principle is always coupled to currents or voltages that change over time (U=L*di/dt).
Air core coil:
Is a special design. The advantage of its largely linear characteristic is offset by its large size and low inductance compared to iron core coils.
Motor choke:
AC inductor, mainly 3-phase, arranged between the inverter (frequency converter) output and the drive motor to shape the motor currents, these inductors extend the service life of the motors and reduce noise. The required inductance values depend, among other things, on the length of the cables between the inverter and the motor.
Star point choke:
Inductor for damping the currents and their gradients in the earthed neutral point (via this inductor) in the event of earth faults in power supply networks (e.g. railway power supplies).
Current-compensated inductor:
These inductors are winded and switched in such a way that they have little influence on the useful signal, but provide effective suppression for an interference signal.
The component size of inductors ranges from SMD components to iron inductors weighing several tonnes for power electronics applications, for example in drive technology (railways).
BREMER Transformatoren manufactures inductors in mechanical dimensions comparable to our transformer production range.
In addition to a few standardised small chokes and line chokes to increase the so-called uk, inductors are mostly developed individually for our customers.
Small inductors up to 50kVAr – or higher by agreement – are described in EN 61558-2-20.
See also: Products Inductors and Flyer inductors